
ABB is one of the major international suppliers of robotics and automation with over 500 000 robotized solutions sold worldwide. A complete range of solutions, avant-garde technology, and immense experience in the sector allows ABB to offer, through its System Integrator, quick, precise, reliable solutions that help companies increase productivity and flexibility in manufacturing lines, guaranteeing and improving quality and safety.
In response to the increase in e-commerce and the need for shelf-ready packaged products, the company has developed FlexPicker IRB 365: the Delta robot with five axes that is the fastest in its category for product picking, packaging, and reorienting up to 1.5kg. By handling more products per minute, up to 120, the IRB 365 robot makes production more efficient while saving time and energy. To speak to us about the new robot and its applications is Nicola Tricomi, Business Development Manager Robotics Division ABB Italia.
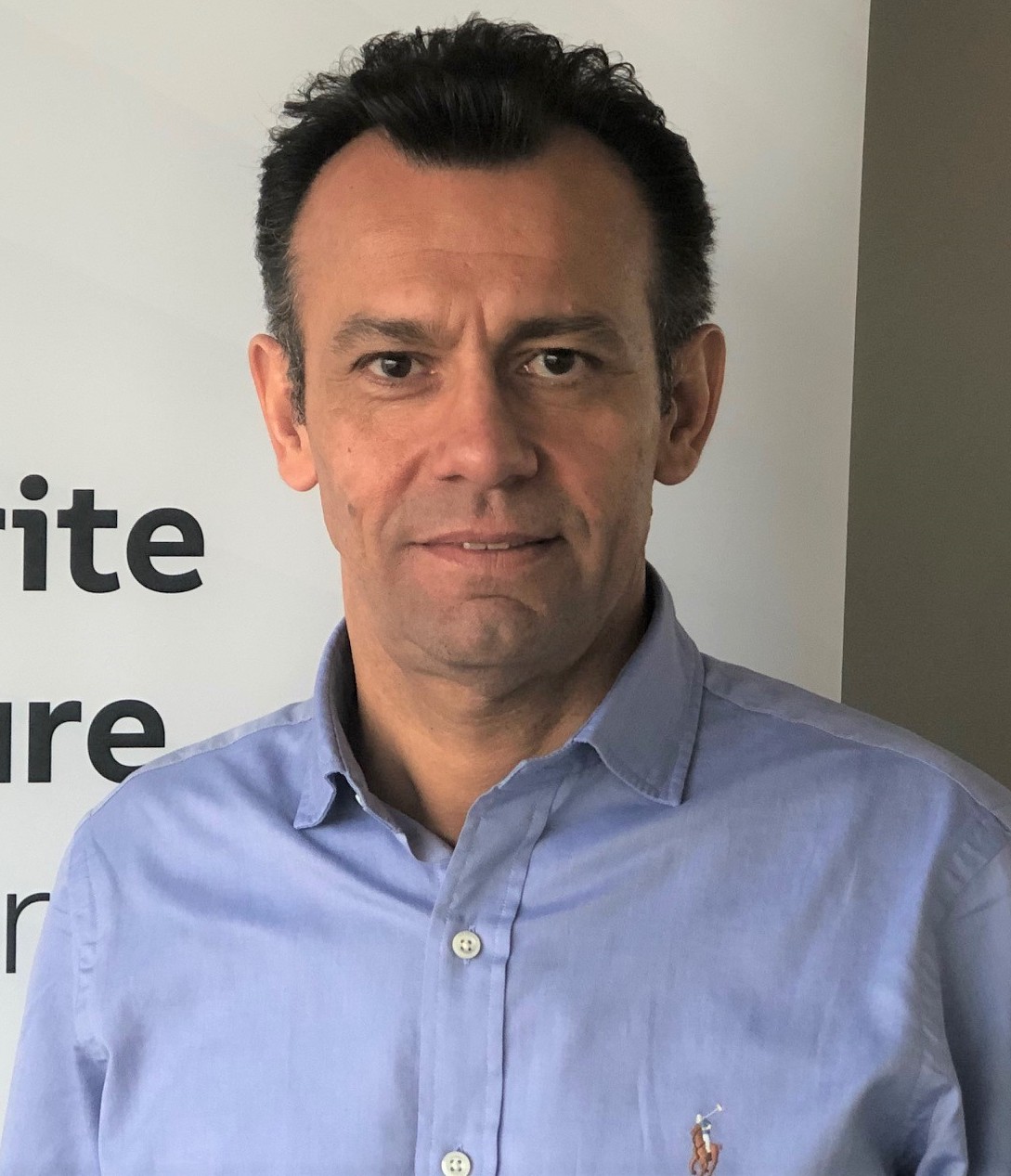
Is ABB already operating in the cosmetic sector?
Yes. ABB has been in the industry for some years now with its System Integrator, which gives companies in the sector innovative and adequate solutions to face the challenges of an international market. Our goal is to continue on this path because it’s a healthy sector with continual growth and one that invests in robotics and automation. 2021’s values that were seen in the Annual Report of Cosmetics Italy confirm the state of the industry which emphasized not only its resilience to the economic crisis but especially its reactivity and ability to adjust to the new purchasing habits of both Italian and international consumers.
Italian manufacturing exceeds 11.8 billion euros and 41% of this is export. The 630 companies that in 2021 produced 90 % of the sector’s entire revenue had invested in machinery and technology for a total of around 300 million euros.
Why should a company trust in ABB?
ABB has a portfolio of technologies that allows us to supply integrated solutions for the entire production chain. From control of the process, quality, and sensitive parameters of product production and of packaging to the palletization and management of logistics using AGV. This transversal approach allows us to be a technological partner for a complete smart factoring solution.
Through AI algorithms based on self-learning systems that update data in real time with ABB control systems, it’s possible to modify the setup of lines optimizing and increasing the performance of the production facility remotely. And there’s more. Thanks to decades on the robotics and integrated automation market, ABB prides itself on having installed around 500 thousand robots worldwide. In addition, through 3 manufacturing sites that are operative and one that is in the start-up phase, ABB is able to satisfy the needs of the market with technologies that are always increasingly innovative, often developed in collaboration with our clients.
What are the biggest challenges in the cosmetics sector?
The competitive challenges to face in the production sector are related to speed, quality control, the versatility of lines, the reliability of packaging lines, the automation of logistics and today, more and more, energy consumption and sustainability.
Today, ABB is the ideal partner to guide companies to increased competitiveness, thanks to its innovative offers of products and systems that cover a wide range of technologies, unique in the automation market.
What uses was the FlexPicker IRB365 designed for?
Over recent years, the acquisition of some companies such as Codian, B&R, and ASTI, has allowed us to provide transversal solutions for production processes, based on the increase of the Delta Robot range, on the supply of advanced solutions for integrated automation and solutions for the automatic handling of products within a company (AGV). FlexPicker IRB365 is one of these.
With its ample range of applications, Flexpicker IRB365 is the response to the growing demand for shelf-ready packaged goods where speed and adaptability of the production line are essential. FlexPicker® IRB 365 is the fastest in its class for picking and packaging applications up to 1.5 kg and, with its 5 axes and operating speed of 120 pieces a minute, it can be used to manipulate different types of products in the secondary packaging phase (ex: containers, bottles, and packages used for the logistics department…)
Thanks to PickMaster® Digital Twin, an advanced software that allows the robot to be virtualized within the plant, it’s possible to carry out all simulations and tests before installation. In addition, thanks to the PickMaster® Digital Twin, it can be integrated into packaging lines in a matter of hours rather than days, reducing commissioning times.
In what way can these product lines be customized?
For example, with Collaborative Robots. Thanks to their versatility and the possibility to utilize them in various applications and carry out installation without needing to modify the layout of a line, Collaborative Robots are seeing more and more interest from the manufacturing industry. Production lines that integrate collaborative robots allow for increased customization and seasonality shifts, increasing the speed of responses to on-demand requests.
The use of Cobots is a solution that guarantees the continuity of production and product quality in full compliance with operational safety. In fact, Cobots are equipped with safety and anti-collision systems, in addition to video cameras and sensors, that allow for the sharing of space with in-line operators without risking accidents in accordance with regulations in force.
For years, ABB has offered clients a range of Cobots, like the dual arm YUMI and the single arm GoFa, to manage solutions in specific and versatile manufacturing processes while fully operating alongside manufacturing personnel. Ultimately, Cobots are also finding applications within shop centers for the preparation of customized cosmetic products.