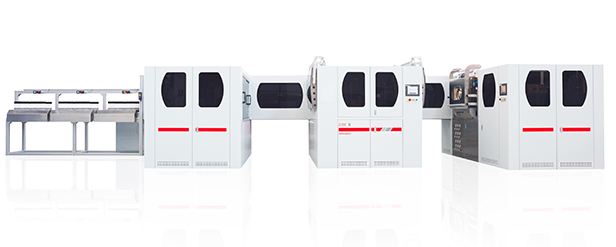
The lengthy months of the pandemic have changed many things in the market, both on the consumer side — giving rise to new consumer habits and heightening awareness of issues such as sustainability and safety — and on the manufacturing front. The supply impasse due to disruption of the distribution chain, which was followed by a spike in demand, has resulted in skyrocketing raw material and semiconductor prices, and thrown the market off balance. A situation that has prompted businesses to seriously consider the need to rethink the supply chain.
“The crisis has highlighted all the fragility of the current system, which is based on dependence on market demand, on external suppliers (often located in other countries, or even on a different continent) and on just-in-time manufacturing,” explains Antonio Scotti, Sales Director at Tapematic.
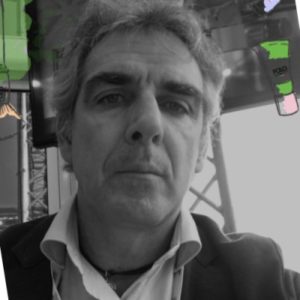
“We see all this as an important growth driver since businesses have realized that the distribution chain needs to be shortened if they are to be independent, have more control over the quality of their products, and also pursue environmental sustainability goals: a shorter supply chain also means reduced impact on the ecosystem. A trend borne out by the growing demand for modular systems that we’ve witnessed in the past months”.
NEXT STEP: MIDDLE EAST
Offshoring to the European market will take time, being a lengthy and onerous process, but the road has been mapped out and many brands — not just European ones — are looking in this direction. A road that’s destined to deliver greater transparency and visibility all across the value chain — something that consumers (and others) are crying out for — and that results in faster response times to market changes, which is good for everybody.
“We saw this just recently in Dubai, too, where we went for BeautyWorld Middle East. The Middle East is a market that might well have some welcome surprises in store, not just because Italian-made technologies are recognized as high-quality products, but also because there’s growing interest in the internationalization of certain processes and our machinery — which is modular and made to order — is designed to meet this very need.”
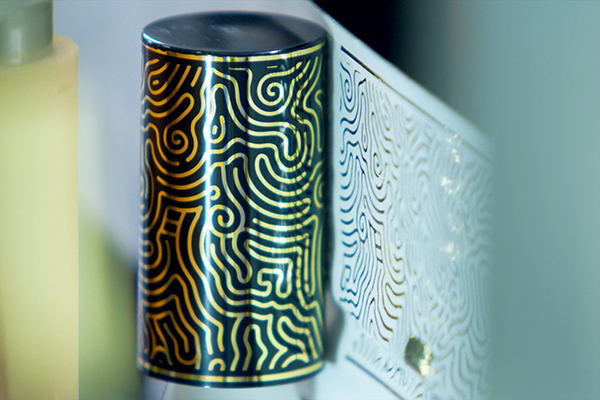
MODULAR SYSTEMS MADE TO ORDER
Systems produced by Tapematic — which has been designing and developing top-quality machinery in-house since 1970 for the UV coating and metallizing of packaging — cater perfectly to market demands. Cutting-edge technologies featuring a high level of automation and digitalization, to offer businesses the ultimate flexibility.
Scott goes on to say, “Our machines are systems that meet the companies’ demand for greater dynamism and agility. Tapematic PST Line, one of our bestsellers, is a system tailored to the customer’s requirements: assisted by our team, the customer chooses which of the various modules on offer best suit their needs, getting a tailor-made product, but for a fraction of the cost of a fully custom machine. There are actually a number of modules available: manual and/or automatic loading and unloading, cleaning and pretreatment, primer, standard coating, metallizing, decorating, top coating and 100% quality control.”
Every detail and every component is easily customized further based on individual requirements, as each line is designed and produced in-house. A factor that makes every system different: “we can safely say that no two lines are exactly the same, instead every system is created ad hoc for the business ordering it.”
TAPEMATIC IDM II, FLEXIBILITY IN DECORATION AND OVERCOATING
With a focus on modularity and production flexibility — key drivers at a time when demands for products and goods are evolving at a rapid rate — in January 2021, the company introduced the market to its latest new offering: Tapematic IDM II. “A decorating module that can be integrated with all modules from the PST II Line, thus achieving a fully automated line that can be used to create countless decorations on packaging of all kinds: hot stamping (sides and ends), laser decoration (sides and ends). This module can also be used to apply a protective UV overcoating so as to improve its performance, prevent possible contamination due to manual handling, and enhance the decoration with an incredible bright effect.”
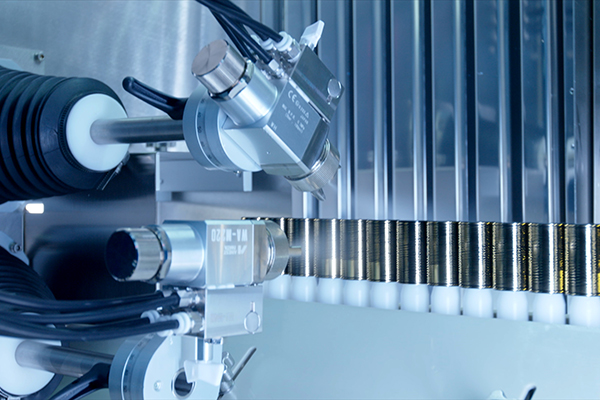
EASE OF USE AND SUSTAINABILITY
For Tapematic, modularity also addresses two of the market’s other growing needs: sustainability and ease of use (and maintenance).
“Another issue that’s come to light with the pandemic is the shortage of skilled personnel. Training personnel is a costly and time-consuming exercise,” Tapematic’s manager finishes off by saying. “Technologies have the advantage of requiring less personnel, thus taking this expense out of the equation for businesses. And then there’s the environmental sustainability aspect, an awareness that’s gained ground among end consumers and businesses alike — one that, for us, translates into two words: use less. Our mantra is use less, use better. And this is exactly what can be achieved with our machines: controlling quality to produce less waste, rationalizing processes and consumption to reduce environmental impact.”